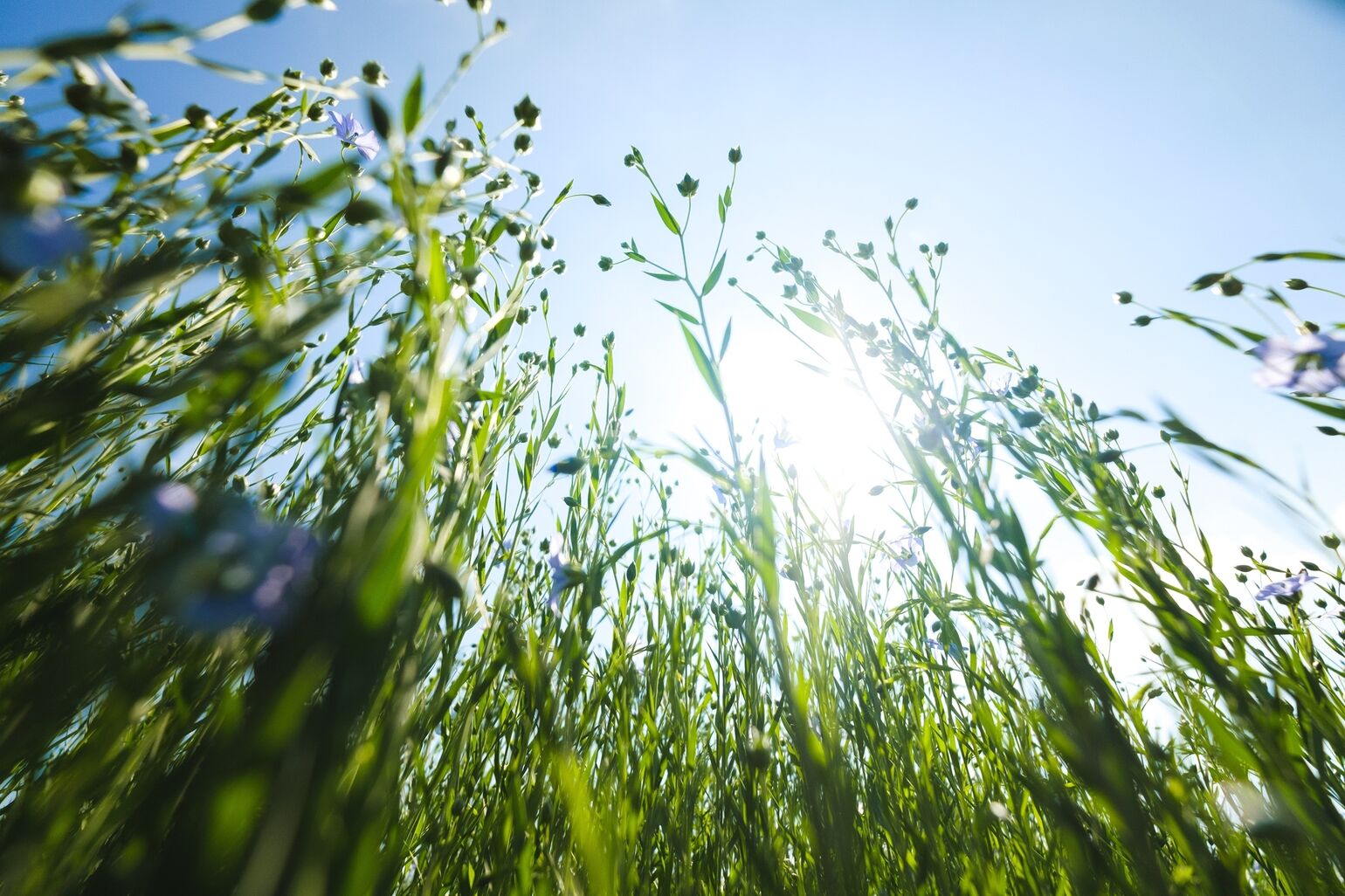
Linen: made from carbon sink flax plants
Jul 18, 2022
LifeWear
An important part of the UNIQLO LifeWear philosophy is the production of responsibly sourced, environmentally friendly fashion. When we make our high quality Premium Linen, we ensure a meticulous level of quality control and a thoughtful manufacturing process in order to provide you with an economically friendly wardrobe staple as a responsible global citizen.
Shop the look: linen shirt and linen blend shorts.
Let's go back to the source and learn a little more about the origin of linen and how our brand new range for women and men is made.
PART ONE: THE PLANT
Shop the look: linen shirt and linen trousers.
Linen all begins with the flax plant. Cultivated across Western Europe, it's the only plant textile fibre that originates on the continent and as such, this cultivation process could not be undertaken anywhere else. The unique combination of Western Europe's natural ocean climate, flax's low thermal density, rich soil and the unparalleled experience of flax agricultural experts all contributes to our superior finished product.
The flax plant is also a carbon sink, as it traps nearly 250,000 tonnes of CO2 every single year. The flax growing process also requires no GMO, no defoliant, no irrigation and only low fertiliser use, making it a naturally sustainable plant to produce fabric from.
Typically, flax is planted between March and April, where it takes approximately 100 days to reach full maturity. In July, the plant is pulled from the ground once the leaves have dropped from the bottom of the stem. The pulled plants are then wrapped in cloth and a process called 'retting' takes place. This is where sun, dew, rain and other micro-organisms work to detach the plant fibres from the stem. Once ready, it's time to gather the fibres.
PART TWO: THE FIBRE
The mechanical process of separating the fibre from the plant is called 'scutching', a practice made up of smaller processes like 'shelling', 'stretching', 'grinding' and 'treshing'. These fibres are separated with mechanical and physical exertion to ensure that no part of the flax plant goes to waste; every single part of flax can be used. Scutching tows can serve as raw material for paper or composite production, shives are ideal for manufacturing chipboards or for animal bedding and linseeds are transformed into oil.
PART THREE: THE YARN
The third part of the transformation process sees these fibres transformed into yarn. After a process of combing which leaves the linen fibres looking like long, lustrous strands of blonde hair, they must undergo untangling, regularising, stretching, threading and spinning. Different techniques and movements can be employed in order to produce different types of yarn. Further processes of weaving, knitting and finishing render the linen ready for use in our elegant shirts, jackets, trousers, dresses and shorts.
PART FOUR: THE EXPERIENCE
The final part of the picture is down to you; sheer enjoyment of a luxurious, precisely crafted fabric which boasts a soft, comfortable texture and rich colouring. Want to see what our linen range has on offer? Explore our linen for women and for men.
TOP